The Engineer’s Guide to Custom Cable Design
Introduction
Custom cable design can be a bit overwhelming, especially if you are like many and left the cable and connector design until the end of the project. There are many different factors that can affect material selection and many different materials to choose from! So how or where does someone even start with designing a custom cable or complete connectivity solution for a specific end application?
As with any project, a requirements gathering session is imperative to designing the right solution for the needs of your device or application. Understanding the application and the environment it has to perform in will help the cable design engineer choose the appropriate components and cable materials.
Requirements Gathering
- Identify End Application
- Application’s Environment
- Time
- Temperature
- Exposure to UV, chemicals and/or oil, water (fresh, salt, waste/treated)
- Frequency of exposure to the environment
- Critical-to-Quality Characteristics
- ‘Needs’ vs. ‘Nice to Haves’
- Flexibility vs. Flex Life Expectations
- Flexibility – suppleness, a measure of how much movement a cable can tolerate at a given time
- Flex life – how often the cable will need to flex at a given radius or defined movement.
Another important aspect of the initial design consultation will be to get an understanding of any existing pain points or performance failures that are occurring, assuming the opportunity is to improve an underperforming design.
When working on a brand-new project, a prototyping phase may be necessary to ensure that the cable solution is performing as expected in the real-world environment.
No matter where you are at in your project, whether there is an existing or new solution, it is recommended to partner with a cable design engineer to ensure your application requirements are met. We designed this White Paper to help get you thinking about the different factors that may affect design and material selection to get you started on the right foot.
COPPER STRANDING
Benefit from Optimal Stranding Materials & Configuration for Your Wire and Cable Application
When it comes to connectivity, proper material selection and stranding configuration aligned with your application affect different attributes such as flexibility, flex life, and termination to the connector to name a few.
When selecting copper stranding, ask:
- What is the primary end-application and use for this cable?
- What environmental factors will this cable need to perform in successfully?
- What approvals or agency certifications are required for the application?
The end application requirements will help determine the following:
- Size of the stranding
- Bare copper vs. coated
- Tin
- Silver
- Nickel
- Gold
- Copper alternatives
- Alloys
- Steel
- Tinsel
- Aluminum
- Stranding configuration
- Concentric
- Unilay
- Rope Lay
- Bunched
Copper Coating
Bare copper is preferred in most situations, though some copper alloys are better suited in environments where excellent abrasion or corrosion resistance is needed. More commonly, copper strands have a coating applied to add the properties required for a given application. For example, tin coating would be a preferred method when soldering is being used. The nickel plate and silver plate come into play when a higher temperature material is being used, such as a fluoropolymer. This is because nickel and silver melt and reflow at a higher temperature.
Copper Construction and Configuration
Copper stranding is defined by both its overall size and an individual strand’s size. For example, a 18 AWG (0.75 mm²) construction would be defined as 16 ends of 30 AWG. Application often determines the size of stranding that will be needed. In a power application, the ampacity requirements for the stranding will define the size needed to handle the power load, considering all the conductors that are in play.
Stranding Designs
Stranding configuration selection depends on the end-application of the cable and the environment in which the cable must perform. Key deciding factors are flex and movement requirements. The typical rule of thumb is “the more strands, the more flexible and the longer the lifespan”. From a movement and motion standpoint, a rope lay construction is by far the most flexible configuration – it is also by far the most expensive, highlighting the trade-offs buyers and engineers must constantly consider when choosing materials.
For static applications, stranding matters less. Dramatic temperature fluctuation does not affect copper as much as movement does, but it is important to consider the connection point and how the cable will be terminated, as this could be a vulnerable area.
Other factors to consider are applicable regulatory agency requirements. As a North American company, Northwire adheres to many guidelines, with UL as one of the most predominant. UL requires twisted stranding in most applications. With other approvals and some agencies, manufacturers can run stranding without twisting it together.
CONDUCTOR MATERIAL
Choosing the right materials for your custom cable can be a daunting task. To help clear up the ambiguity and to get you started on choosing an appropriate conductor type, we have laid out some information below on the eight most common conductors and the benefits of each. Keep in mind that it is important to consider the end application and its environment when choosing any custom cable material.
Bare copper
Bare copper is the most commonly used conductor type and is preferred in most applications because it is highly conductive and very cost effective. Offering a pure signal over long distances, bare copper also has natural flexibility and high tensile strength. With a temperature limit of 150°C, it is not the best suited for high temperature applications. If high temperature performance is required, silver or nickel-plated copper may be a better choice.
Tin-plated
If the custom cable or cable assembly will be used in a wet environment and corrosion resistance is a requirement, then tin-plated copper is a good conductor option. Another cost-effective solution, tin plating is also easy to solder and can withstand up to 150°C.
Silver-plated
The low oxygen content and conductivity makes silver-plated copper an excellent option for audio cable due to the purity of the copper and the lack of tarnishing. Other benefits include solderability and a higher temp rating up to 250°C.
Nickel-plated
Nickle-plated copper is often used in high temperature applications due to its ability to withstand up to 450°C. In addition, the nickel plating offers corrosion and wear resistance.
Alloys
Alloys are a combination of 2 or more metals. Silver, nickel, copper, beryllium, cadmium, RoHS-compliant chromium are selected for their overall toughness, break strength, and flex-life. Alloys are another great option for high temperature applications.
Steel
Steel is not a great conductor unless coated, but it is extremely strong and has less stretch than other conductor materials. Due to its high tensile strength and crush resistance, steel is often used in military and aerospace/defense applications.
Tinsel Wire
Tinsel wire has high mechanical flexibility and is often used in low current applications such as telephones, headsets and other small appliances.
Fiber Optic
Optical fibers are well suited for light and signal transmission at high speeds, but do not conduct electricity. If flexibility is a concern, plastic optical fibers may be selected over glass optical fibers as glass fibers are very rigid and brittle.
Something to keep in mind is that the strength and flexibility of the conductor and overall cable really depends on the stranding configuration.
SHIELDING
Shielding provides protection to cable and wire by increasing both structural integrity and signal integrity. The primary types of cable shields include a foil shield, a box weave or basket weave braid shield, and a spiral shield.
Functions
To understand the true value of shielding it’s important to know the properties it offers.
Reduce Interference
The most effective shielding against interference is a combination of braid and foil shields. From an electrical standpoint, foil will guard against high frequency noise and a braid will guard against low frequency noise. A combination of the two is ideal for signal integrity.
Increase Flex Life
Foil provides a layer of shielding without adding a lot of weight or cost, but when high flex life is required, it may not be the best material. A spiral shield provides more flexibility, but may have a shorter life span in high flex environments. A box weave, while stiffer, will stay together throughout the flex life of the application due to its interlocking nature.
Act as a Barrier
Tapes, wraps, and separators serve as barriers between a cable’s core components and the outer jacket material so that they do not bond together. Shields protect the integrity of the stranding and increase the resistance to damage, noise, and moisture.
Material Options
Each material and type of braid brings different properties and strengths to the table. Configurations to isolate and separate internal components are very customizable.
Foil
- Protects components and/or entire core
- Reduces cross-talk
- Flexible
- Lightweight
- Cost effective
- 100% coverage
- EMI Protection
Drain
- Easy termination
- Grounding
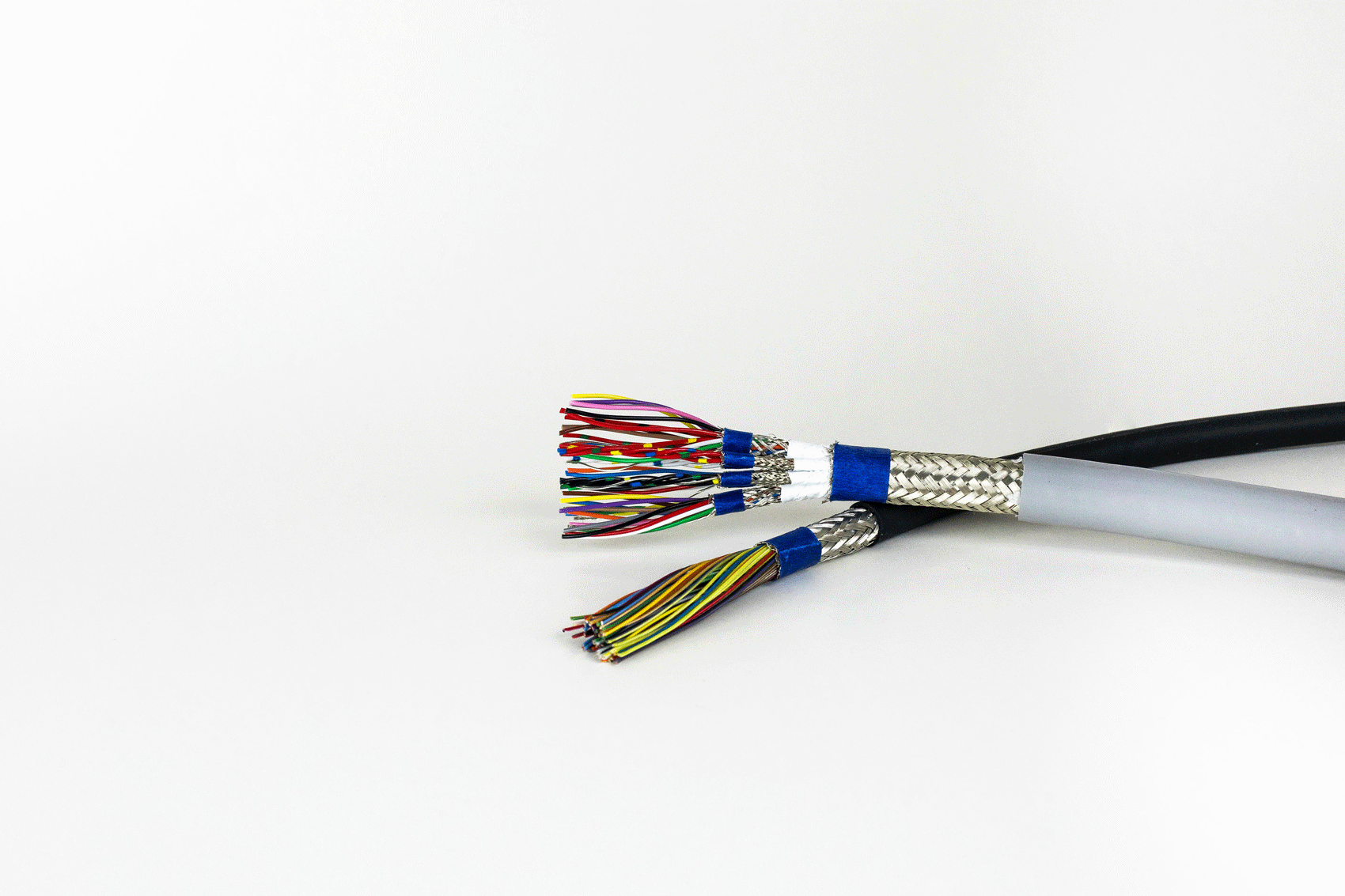
Braid
- Superior structural integrity & physical protection
- Higher flex life
- Mechanical strength
- Slower process
- Can be difficult to terminate
- Reduces cross-talk
- EMI Protection
If your cable is failing due to electromagnetic interference, a short flex life, or too weak of a structure, shielding might be just what you need.
Ruggedize your cable with shielding
Shielding provides protection by increasing both structural integrity and signal integrity. Selecting the right shielding materials and configurations can add strength, flexibility, and noise suppression.
- Materials like Kapton® tapes are designed specifically for high temperatures while Polyester excels in low temperatures
- Aluminized backing can be used for shielding and insulation
- Binder wraps hold components together to make sure tensions stay the same
- Based on coverage and material, tapes can increase flex life or rigidity
- Wraps and tapes can be designed to protect from moisture and chemicals
TAPES, WRAPS, AND FILLERS
Does your cable need increased flex life? Will it need to perform in extreme temperatures? Worried about crosstalk? These concerns can be addressed with the addition of tapes, wraps, and fillers to your custom cable design. There are many different tape and filler options that are available. Some of our more commonly used materials are listed below, but there are additional materials that can be utilized depending on your unique application’s needs. These material options can be applied at various operations to achieve a range of functions and offer several benefits, including the following:
Tapes & Wraps:
- Offer noise suppression or eliminate cross-talk between inner components
- Add shielding and isolation
- Increase flex life
- Provide water blocking
- Provide flame retardancy
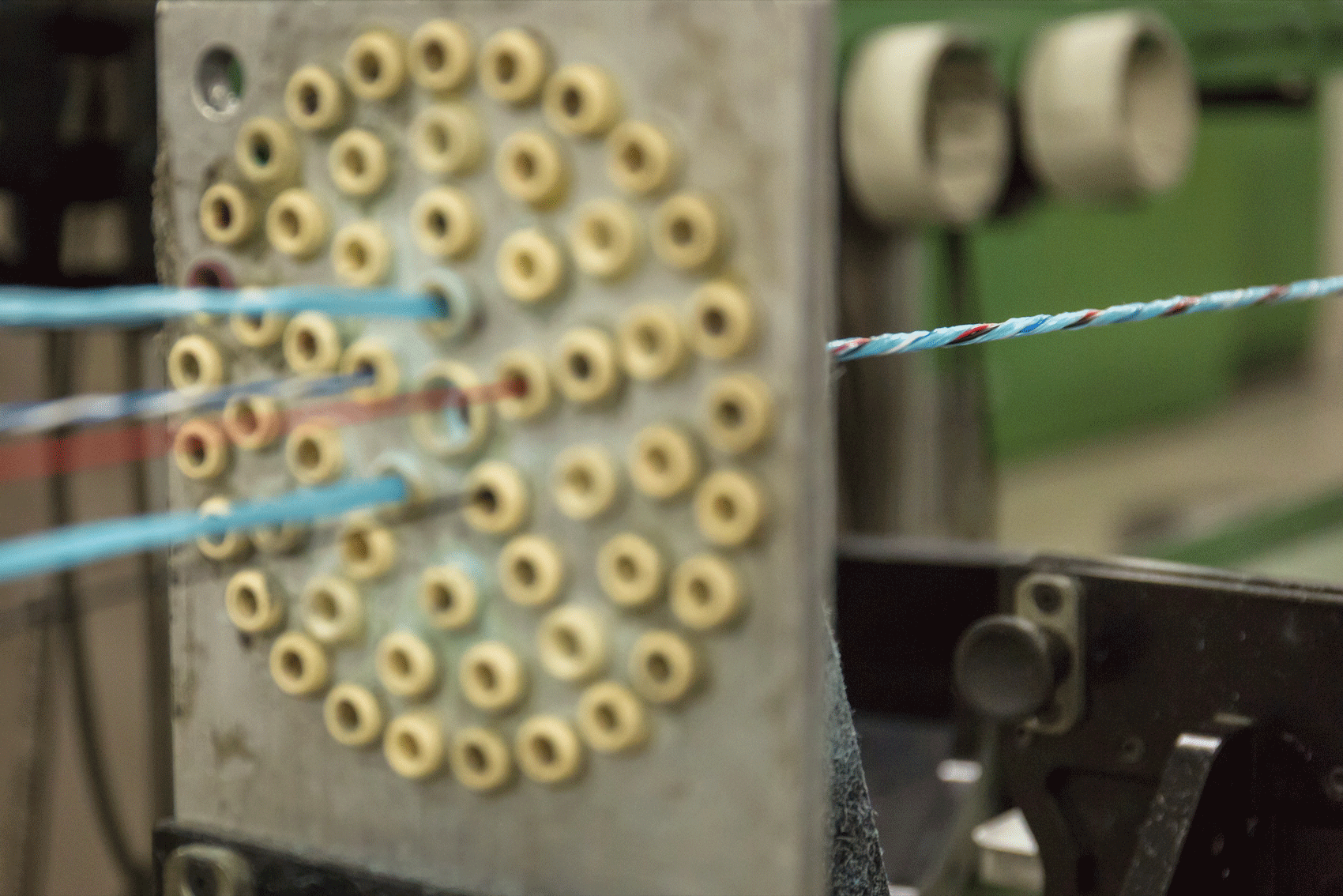
Commonly used materials for tapes and wraps:
Paper
- Separator between core and jacket
- Light weight and flexible
- Least expensive
Mylar (polyester)
- Binds components or entire cable
- Opaque, clear, or aluminized
- Cost effective
- Less flexible
Spun Nylon
- More flexible
- Light weight
- More expensive
PTFE
- Most expensive
- Superior flexibility
- Chemical
- ePTFE (expanded PTFE)
- Insulating capabilities
- Sintered/Unsintered
Kapton
- High temperature properties can be aluminized for shielding purposes.
Polyester
- Buffer or separator
Aluminized Polyester
- High frequency shielding
Foamed Polypropylene
- Buffer or separator
- Added mechanical properties against crush/impact.
Fillers are often times used due to one of the following:
- ‘Fill in’ gaps to make a cable round and more aesthetically appealing
- Increase flex life depending on coverage and material used
- Protect from moisture and chemicals
- Easier molding and sealing in glands
- Water blocking options available
Filler materials:
- Polyolefin
- Cotton
- Extruded thermoplastics
- Strings and yarns
If you are looking for more than one function in your tape, wrap, or filler, do not fear. These are very customizable and their coverage can range from full to minimal depending on your needs.
If a long flex life, insulation, moisture protection, or extreme temperature consideration is something your cable needs, a tape, wrap or filler might be a good addition to your custom cable design.
STRENGTH MEMBERS
Strength members add support to preserve cable integrity and help the cable withstand different types of movement.
What is a strength member?
A strength member is the component of a cable with the function of adding support to preserve the cable integrity. Strength members add both function and protection to connectivity solutions. There are several options including steel, aramid fiber, or a stiff fiberglass rod that runs the length of the center of the cable. The strength member helps the cable withstand different types of movement including:
- Pulling
- Torsion
- Continuous
- Variable
- Bending
- Rolling
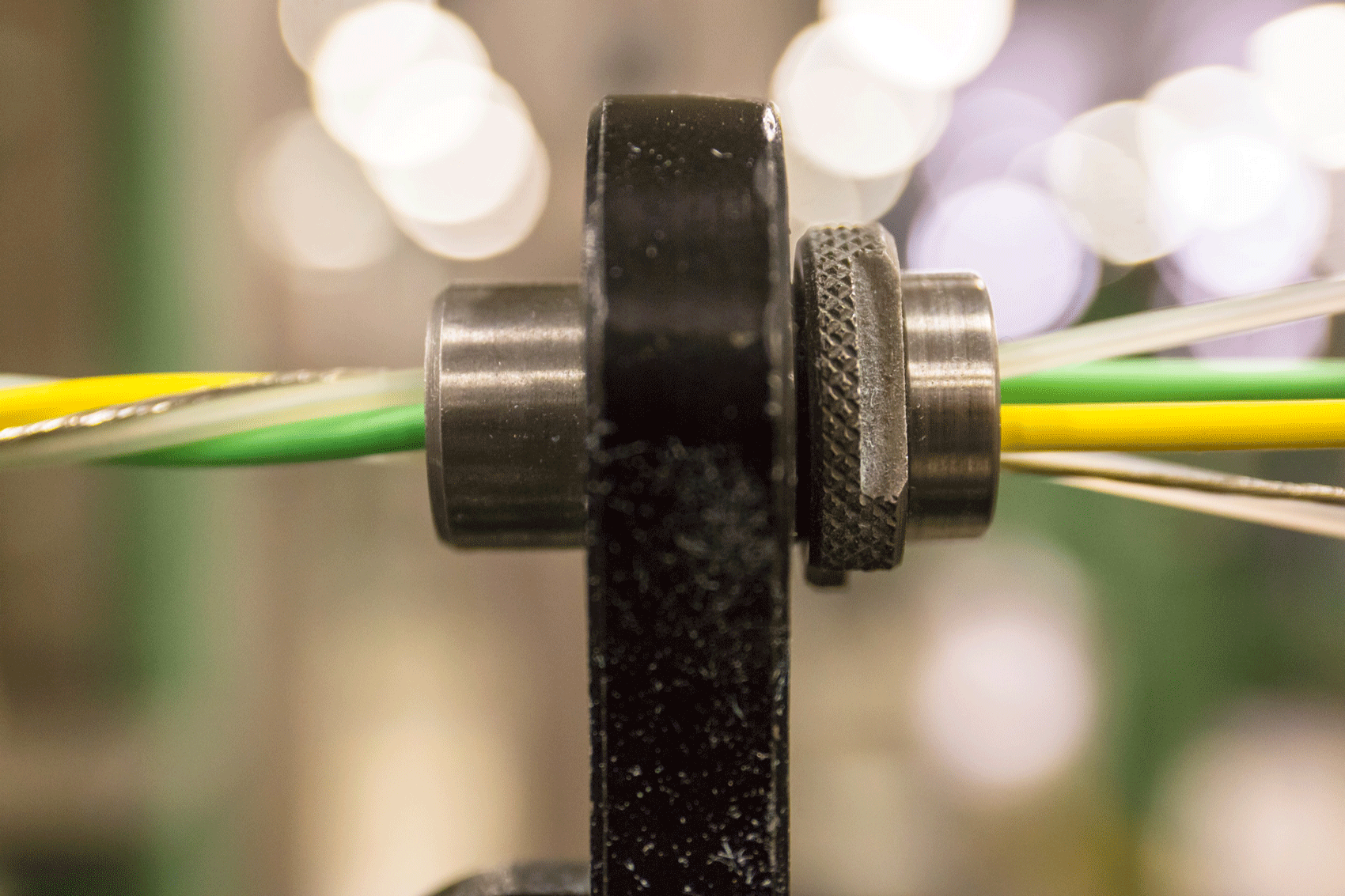
Why do you need a strength member?
Cable that is expected to perform in tough or rugged environments can benefit from the reinforcement that strength members offer. The strength member core makes sure that there isn’t pull on the connector. They offer support and add longevity to the cable.
How do you select a strength member?
When deciding what material and type of strength member ask yourself three questions:
- What is the pull strength requirement?
- Does this cable need to be flexible?
- Does the strength member need to be terminated to the connector?
- Is cable weight a concern?
Aramid Fiber
Kevlar® is a brand of Aramid fiber and a strong material ideal for extreme pulling strength. Aramid fiber can be stranded in a variety of configurations to achieve differing levels of strength. For example, a bundle of four strands provides 450-600 Newtons of pull strength. While it is not rigid, it does offer high compressive strength without adding significant weight. If aramid fiber is used in a cable solution, special attention must be given to the cable’s termination, as incorrect termination can lead to weak points in the fiber.
Steel
Used in applications where pulling strength and compressive strength are critical. There are different types of steel strength members that may be used depending on weight requirements and durability. Stainless steel strength members provide excellent strength at just 3/16th of an inch. Galvanized steel provides pull strength of about 500 Newtons without breaking, along with superior compressive strength.
Fiberglass Rods
Extremely rigid and good matches for pulling or pushing applications. The fiberglass has great compressive properties and is very strong. It is important to consider the environment since fiberglass cannot handle extreme heat or cold. It cracks below -20°C and above 80°C.
TUBES
Whether supplying air, dissipating heat, or suctioning fluids, tube material choices can make a big impact on cable performance. Depending on the environment and the demands of the application, the tube could be at risk of collapsing, kinking, or even being too rigid and preventing flexibility. Cable Designers will consider the following factors when designing your cable to ensure the overall construction and its internal components function flawlessly.
When selecting tubes, a Cable Designer will ask a few questions, including:
1) What is the primary purpose of the tube?
Typically, something needs to pass through the tube, which will influence what material is chosen
- If the tube will be supplying or suctioning fluid, what type? Chemicals? Water? Other?
- Some tubes are designed into a cable to supply air. If this is the case, is it ambient air, oxygen, or another type of gas?
- Is it a vent to dissipate heat, pressure, or steam?
2) What are the desired cable features?
Knowing the demands that will be put on the cable will help determine the best durometer
- If the cable must be highly flexible, a designer will choose a tube material that is rigid enough that it won’t kink or collapse, but not too rigid that it feels stiff.
- Specific bend radius will be taken into consideration to ensure the cable will have a high flex life if needed.
- Type of termination and connector choice also affect design.
- Will there be an over-mold? Added pressure could cause the tube to collapse if improper materials are selected.
3) What type of environment will the cable be exposed to during the lifecycle of the application?
Features such as flexibility can also be affected by the external environment, so it is important to disclose this when starting any cable design
- If the cable will be in a wet environment, it is important to know what type of fluid such as type of water (salt, potable, etc.), chemical, or other.
- Extreme temperatures including high heat or extreme cold could affect cable performance if the right materials are not chosen up front.
- If the cable will be in a medical environment, then a medical-grade tube may be required.
JACKETING
A cable’s outer jacket is its primary means of protection against environmental factors and application demands. It is a crucial part of the cable and can be the determining factor for the longevity and durability of the cable and or cable assembly. Choosing a jacket material can seem like a daunting task, but do not fear, we put together a few questions to get you started.
As with any material choice, it’s important to understand the end application, its environment, and whether it requires approvals.
End Application
The application is the number one influencing factor when selecting materials for any component of the cable. Certain specifications or characteristics may be determined by the end use. For example, if the cable will be in a medical device, the jacket may need to be biocompatible and/or sterilizable, which will quickly narrow down the list of material options.
Environment
Material options will differ depending on the environment that the cable and end application will be exposed to such as extreme temperatures or continuous flexing. Furthermore, time, temperature, and frequency of the exposure to the environment, and exposure to UV, chemical, oil, and water will be important to know as well.
Approvals
If the cable needs to have agency approvals, such as UL, CSA, DIN, etc., the materials that can be used will be selected depending on those requirements.
Will the connector be over-molded to the jacket?
- It will be important to consider both the over-mold material and the jacket material as you will want to ensure that they will adhere to each other.
- In addition to material consideration, shape is an important factor as well. If the cable assembly includes an over-mold, the cable must be round to ensure a clean shutoff.
Does the assembly process involve jacket stripping and if so, to what length?
- When evaluating jacket materials, you will want to factor in any downstream processes such as stripping. It’s important to consider what tooling will be used as some materials are easier to work with than others. For example, a polyurethane is more difficult to score and strip than a PVC.
- The method used to apply the jacket can have an impact on jacket removal.
Ruggedize your cable with jacketing
Jacketing is the first line of defense. Jacketing protects against environmental factors and application demands. Each jacket material offers different properties and special material blends can be compounded to meet performance needs. An application engineer will work closely with you to identify the best jacket solution, for example:
Fluoropolymers
Fluoropolymers are excellent for withstanding extreme temperatures as well as cut, crush, and/or abrasion resistance as the material maintains rigidity even in high temperatures
TPU
A TPU (Thermoplastic Urethane) material is a good option in abusive environments where chemical resistance is needed. It is also an excellent choice for a retractile cord
TPE
If flexibility is important, a TPE (Thermoplastic Elastomer) material may be considered. It is a softer alternative which maintains strength and damage resistance making it a good option for coil cords as well.
FLEX
Given how many cable assemblies are required to tolerate movement – whether small amounts during initial installation or repetitive daily motion – understanding the flex requirements of a given application is crucial to choosing the right wire and cable. When looking at cable types, terms like “flex,” “flexibility,” and “flex life” show up often. Within the world of “flex,” flexibility and flex life may sound equivalent, but there are key differences. In fact, some high flex cables can have short flex lives, and other wires and cables with high flex life may not be particularly flexible.
Flexibility
Simply put, flexibility is a measure of how much movement a cable can tolerate at a given time. Flexibility comes in many types: torsional, rolling, bending, and variable. When a cable is bent, twisted, or pulled into positions other than its original state, its flexibility is tested. Flexible cable can bend significantly and stay bent for a large amount of time without being damaged. A very flexible cable can be compared to the flexibility of a “wet noodle”.
Will your cable need to be bent or curved around an infrastructure? If so, you may need a high flex cable, or cable with strong flexibility.
Flex Life
Flex life deals less with how the cable moves, and more with how often it can move in various ways without taking serious damage. Many cables can bend to some degree for limited use (e.g., installation). High flex life cables can bend repeatedly and regularly without disrupting the cable’s intended use, such as power supply or data transfer.
Will your cable be subjected to repeated movement as is needed in robotics? If so, you may need a cable with a high flex life.
Ultimately, the distinction comes down to use and application. If your cable needs to move well, it must be flexible. If your cable needs to move often, it must have a high flex life. In many applications, such as industrial machinery or factory automation, both flexibility and high flex life are required.
As you have probably gathered by reading this white paper, it is helpful to consider flex requirements up front as all the internal cable component materials will be selected based off those requirements as they can all affect flex.
RETRACTILES
There are numerous applications and unique environments that can benefit from a retractile cord rather than a common straight cable. Here are a few examples that we come across quite often:
High flex life applications
- If the cable will be used on a robotic arm or a security camera where torsional and rotational movement puts demands on the flex life of the cable, a retractile may be your best option as the coil will relieve much of the stress.
Reduce trip hazards
- Worried about cords laying on the ground and possibly tripping an employee or worse, a customer? A retractile cord may be a good consideration as the retractile will snap back into place after use.
Hand held tools
- Coil cords also work well in many hand-held applications. For example, if a tool like an electric screwdriver is used often on a manufacturing line, but needs to be kept out of the way, a retractile coil cord would be the perfect solution.
One size fits all
- Do you have an application that requires adjustments depending on the operator? Perhaps something needs to be adjustable either vertically or horizontally? A coil cord will quickly allow for adjustments without adding any additional cable to get in the way.
Space Saver
- Speaking of cable getting in the way…Working in tight spaces? Utilize coil cords to eliminate the amount of cable that needs to be contained in a cabinet or within a helmet.
Now that we have listed a few examples of when a retractile cord may be preferred over a straight cord, let’s talk about considerations for customizing your coil cord. These are some factors to keep in mind when contacting a Cable Designer as it will help them choose the proper materials.
Environment – Will the cable be exposed to extreme temperature, UV, chemical, oil, or water?
Application need – Is a retractile being considered because the application or part of the application needs to be able to extend and retract or is it more of a rotational need.
Retracted vs. Extension lengths – Northwire can offer different Retracted:Extended ratios. Our standard ratio is 1:5. So, for example, if a cable is 5 feet when retracted, it can extend up to 25 feet.
Tangent direction and length – Parallel (axial) vs. drop (tangential).
Overall diameter of the coil or coil O.D. – This will determine what size mandrel is utilized. The overall diameter is also based on whether the coil cord will be routed over or inside something. For example, a coil cord may be routed on the outside or inside of a telescoping tower mast.
TERMINATION
“What makes the best termination, solder joints or crimp connection?” This is an age-old question with which you will find a myriad of opinions.
Typical prototyping leans toward soldering because of the low cost of entry and re-workability. Whereas high-volume production leans toward crimping with its controllable process and easy learning curve, resulting in lower labor costs. Crimping is also typically better for high amperage or voltage as soldered joints can weaken over time or produce corona discharges
To help you make your decision we assembled a list of pros and cons.
Crimping Terminations
PROS
- Easy learning curve
- Controllable process. Example: Crimp height control charts
- Gas tight termination
- Faster termination- easier to automate
- Good for both high and low volumes
- Best for high amperage or voltage
CONS
- Higher cost of entry
- Low flexibility- due to the need for exact wire and terminal size matching
- Difficult to re-work
Solder Terminations
PROS
- Low cost of entry
- Flexibility- wire gauge and terminals do not need to match exactly
- Easily re-workable
CONS
- Requires a skilled workforce, inexperience can lead to wire and conductor damage
- Non-controllable process
- Difficult to determine a bad solder joint
- Not suited for high volume production
- Flux contamination leading to electrical issues
- When it comes to high amperage or voltage soldered joints can weaken over time or produce corona discharges.
CONCLUSION
As you have probably gathered after reading through this white paper, understanding the end application and environment it needs to perform in is imperative to the overall connectivity design. This information will help guide the cable engineer to select the most appropriate materials to ensure optimal performance.
Now that you have a better idea of how different material options can affect the connectivity of your device and how those various materials are chosen, hopefully your next custom cable design project will be smooth and swift. Knowing the information that is needed upfront to start the design process will make a big difference in the timeliness of a design as well as minimizing unnecessary back and forth communication.
Northwire, Inc. is your responsive partner in the design and development of custom interconnectivity solutions. Whether you have a napkin sketch or fully identified solutions, our cable design experts are available to help ask the right questions in the requirements gathering phase and select proper materials to optimize form, fit, function, and of course, cost! The earlier a cable design engineer gets involved in a project, the better for mitigating the risk of missing your project deadlines!