Twist and Flex Cable for Robotic Applications
Customizing robotic cable from the inside out for lasting performance
In the design of industrial robotics for a manufacturing environment, it is critical to maximize efficiencies and output while eliminating or minimizing down time.
Are you designing your next robotic application? Remember to consider the connectivity of your robot early in the requirements gathering phase. Great questions to consider are: What function will your robot perform? What stressors will the robotic cables endure? What will the environment be like?
Understanding your robot’s function, stressors, and environment will help a Cable Design Engineer help you select the right materials and components of your robotic application for optimal performance.
Requirements Gathering
Identify the Robot Type
- How will the robot move and how often?
Robot’s Environment
- Amount of time of exposure to extreme temps or liquids
- Temperature where robot needs to perform
- Frequency of the exposure
- Concentration of any liquids or chemicals
Critical-to-Quality Characteristics
- ‘Needs’ vs. ‘Nice to Haves’
Flexibility vs. Flex Life Expectations
- Flexibility – suppleness, a measure of how much movement a cable can tolerate at a given time
- Flex life – how often the cable will need to flex
Underperformance of Existing Design
- What are the pain points?
- What are the performance failures?
Through requirements gathering a Cable Design Engineer can evaluate and make recommendations about materials and components for optimal cable performance of your robot.
Designing Cables from the Inside Out for Flexibility and Flex Life
Inner Cable Conductors
Stranding configuration can make a big difference on the conductor flexibility and durability, contributing to flex life.
Stranding Design
Rope lay stranding design
A rope lay is made up of a number of individual bundles of stranding twisted into groups that make up one larger, solid configuration. A rope lay stranding design is the most flexible option, but will also be the most expensive.
Concentric stranding design
Concentric stranding is made up of a solid conductor running down the center that is surrounded by layers of rotating strands. Each layer is comprised of strands running the same direction, but the direction alternates for each layer. Concentric stranding with a high strand count is flexible and holds up to repeated flexing demands or a longer flex life.
Conductor Material Selection
Aside from the stranding configuration, material selection makes a difference on overall flexibility and flex life.
Bare copper
Bare copper is the most commonly used conductor type and is preferred in most applications because it is highly conductive and cost effective. Offering a pure signal over long distances, bare copper also has natural flexibility and high tensile strength. With a temperature limit of 150°C, it is not the best suited for high temperature applications.
Copper stranding will be more flexible with a higher strand count.
Silver or nickel-plated copper
A better choice if high temperature performance is required.
Alloys
A combination of two or more metals: Silver, nickel, copper, beryllium, cadmium, RoHS-compliant chromium are selected for their overall toughness, break strength, and flex-life. Alloys are a great option for high temperature applications.
Strength Members
Strength members help add support and preserve the integrity of the cable through pulling, torsion, bending, and rolling.
Aramid Fiber (such as Kevlar®)
A strong material ideal for extreme pulling strength while maintaining flexibility and flex life. Aramid fiber can be stranded in a variety of configurations to achieve differing levels of strength.
For example, a bundle of four aramid fiber strands provide 450-600 Newtons of pull strength. While it is not rigid, it does offer high compressive strength without adding significant weight. If aramid fiber is used in a cable solution, special attention must be given to the cable’s termination, as incorrect termination can lead to weak points in the fiber.
Separator
Serves as a barrier between the cable’s core components and the outer jacket material, so they do not bond together.
Flex facilitating tapes, such as PTFE or spun nylon, help increase flexibility and flex life. These tapes can be wrapped in-line with jacketing and help the cable flex without compromising the cable structure. It also protects the cable from repeated flexing in a demanding, high flex life application like a robotic arm.
Shielding
Provides protection by increasing both structural integrity and signal integrity. Selecting the right shielding materials and configurations can add strength, flexibility, and noise suppression.
Primary shielding types:
- foil shield
- box weave or basket weave braid shield
- spiral shield
Reduce Interference
The most effective shielding against interference is a combination of braid and foil shields. From an electrical standpoint, foil will guard against high frequency noise and a braid will guard against low frequency noise. A combination of the two is ideal for signal integrity.
Increase Flex Life
In a demanding application like an industrial robot that is constantly moving and flexing on several different axes, a more robust shield like a box weave braid would be recommended. A box weave, while stiffer, will stay together throughout the flex life of the application due to its interlocking nature.
Cable Insulation and Cable Jacket Materials
When selecting insulation and jacketing materials for robotic applications requiring cable flexibility, choose materials with a high dielectric strength and low durometer.
A higher dielectric strength allows you to extrude a thinner wall, which means there’s less material in the way, making it more flexible.
Additionally, choose a softer material with a Shore A durometer of 80 or lower. The softer the cable, the easier it will be to bend and flex. A thinner wall and softer material increase the cable’s suppleness.
Retractile Coil Cords
Many industrial robotic applications utilize retractile coil cords. For example, the retraction and extension might be beneficial on a tabletop type of robot where the arm moves up and down repeatedly. The retractile allows the extension and retraction while keeping the cable out of the way.
In an application where a robotic arm moves up and down and rotates at the same time, a retractile coil cord is added for increased flex life. The retractile section manages the rotational movement while protecting the inner cable components from wear and tear while preventing cable failure.
Learn more:
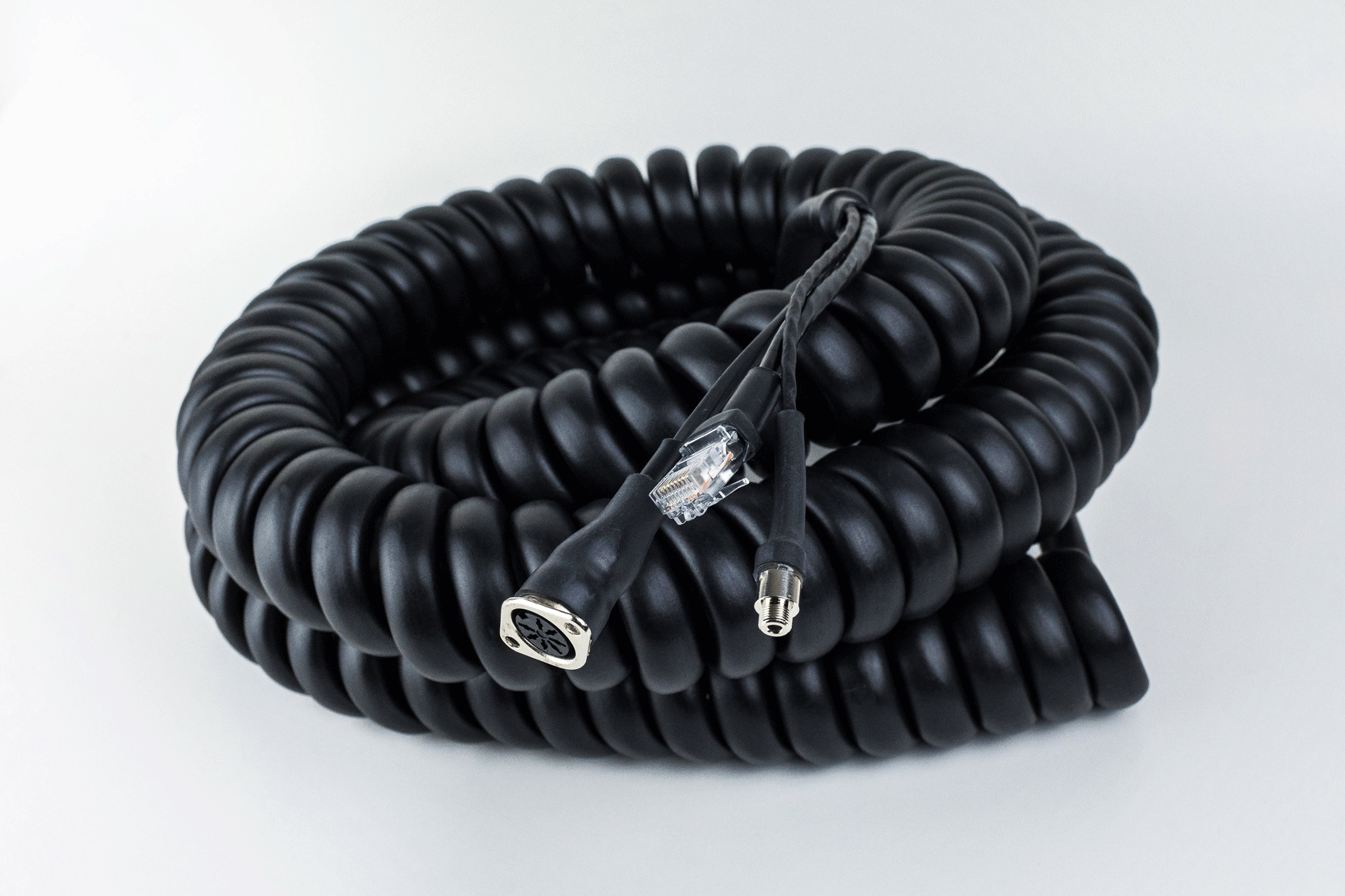
Assembly
When flex is a critical factor, there are many options to consider when it comes to terminating your cable to a connector.
An over-molded strain relief provides longer flex life for your assembly than a boot. The over-mold offers added protection from flexing near the connector or pulling from flex demands further down the cable.
A service loop inside the connector offers a buffer to help prevent conductors from being pulled out of the pins.